Technology
ENERGYN Core Technology
Extreme Technology
Energyn has secured the optimal recipes
for ultra-high-pressure, ultra-high-temperature, ultra-low-temperature, ultra-vacuum,
and rapid heat control processed through several R&D projects
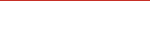
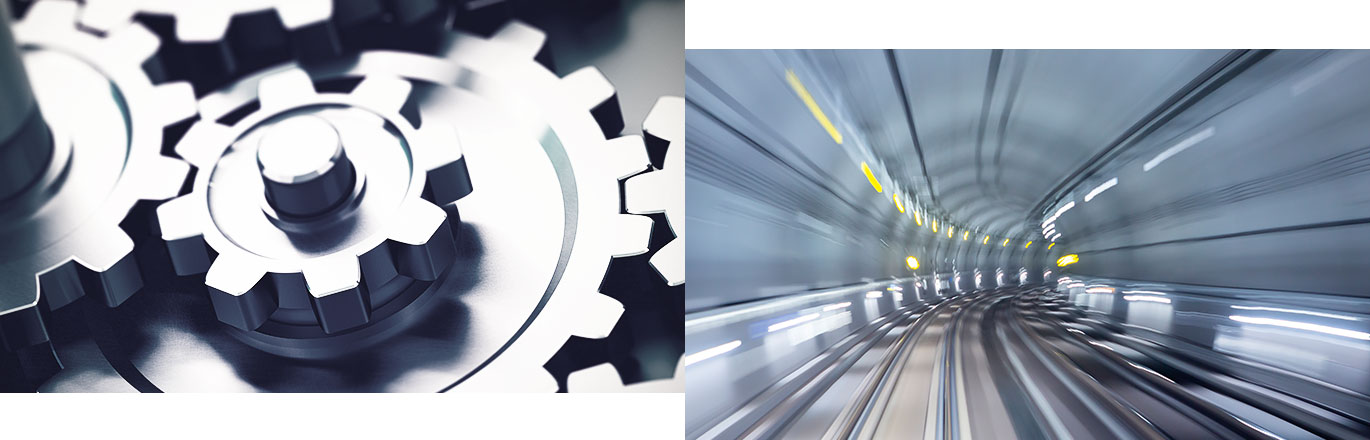
Energyn technology | Ultra-High Pressure | Ultra-High Temperature | Cryo Tech • Ultra High Vacuum | Rapid thermal controlling |
---|---|---|---|---|
Producing ability | 6000 Bar supported (which is the case with only the top three companies, including ‘A’ company in Sweden and ‘K’ company in Japan, etc.) | Liquid (water) 250℃ or higher (Energyn only) Gas 2500℃ or higher |
Liquid hydrogen, liquid helium technology | Rapid temperature change 10~20℃/min (Energyn Only) Reduces the cooling time in a high-pressure environment 1/30 or higher. |
Standard | 3000 Bar or higher. | Liquid (water) 100℃ or higher Gas 2000℃ or higher |
About -271℃ or lower 10(-8)Torr ~ 10(-12)Torr | No common standard (new technology) |
Applied technology | Ultra-High Pressure | Ultra-high pressure •ultra-high vacuum |
Ultra-high pressure •medium temperature |
Ultra-high pressure •high temperature •rapid heat control |
Ultra high temperature •ultra low temperature •ultra high vacuum |
---|---|---|---|---|---|
Applied product |
CIP (Cold isostatic Press)
~6000bar ceramic, metal powder isostatic forming machine
HPP (High Pressure Processing)
Non-heating sterilization equipment through a max. 6000Bar ultra-high-pressure process
|
High Vacuum Hot Press
A machine to perform diffusion bonding or pressurized sintering at max. 3,000℃, max. 500ton, by uniaxial or positive pressurization
|
WIP(Warm Isostatic Press)
max. 6000Bar, max. 80℃ (water) 150℃ (oil) heated isostatic forming machine
|
ERIL(Energyn Rapid Isostatic Laminator)
A laminator with the world’s best rapid temperature change functionality
HIP (Hot isostatic Press)
A high density and high strength processing machine for powder-formed products at max. 2000bar, max. 2000℃
|
diffusion bonding
Binding between materials between composite materials that are not optimal for sintering through sintering or expansion
PCHE
A high-efficiency heat exchanger built by expansion-binding multiple thin layers
|
Wire Winding Technology
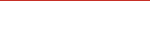
Wire winding technology is the only process technology allowed by ASME* when manufacturing high-pressure vessels of 68.9 MPa or higher, and it is a technology that only a few companies in the world can do. Energen has developed its own wire winding technology that satisfies all certification requirements with years of process know-how, and is actually applying it to high-pressure container manufacturing. The leak before burst design ensures a safe operating environment and maximum durability of the pressure vessel.
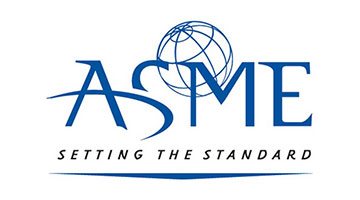
*ASME CODE
A set of technical standards for the designs, manufacturing, and inspection of boilers and pressure vessels was enacted by the American Society of Mechanical Engineering in 1919.
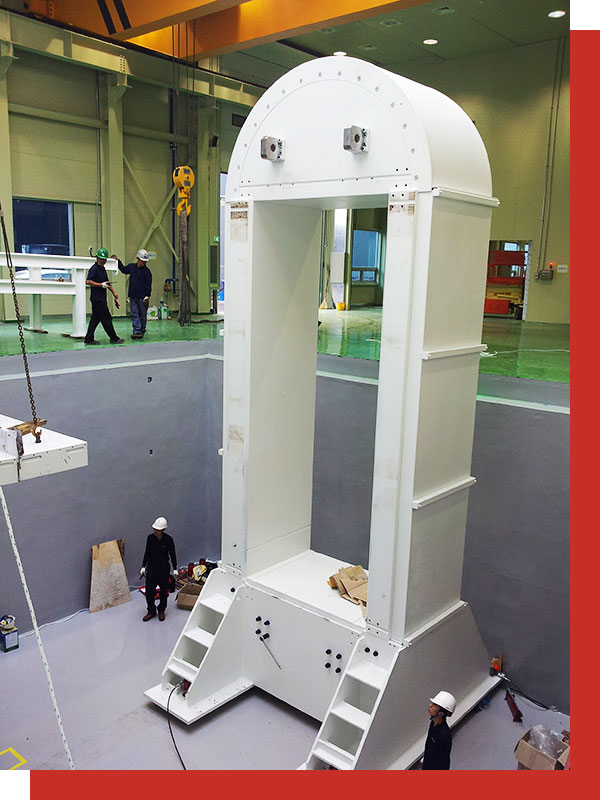
Actual applied to EPCIP-1400
wire winding yoke frame
Characteristics
The frames and bezel of existing presses were composed as an assembly of welded structures or Tie-rods. As a result, they were bulky, heavy, and exposed to tensile stress during operation. A faulty material, in this case, may cause a proliferation of cracks and result in destruction. This put a limit on the maximum capacity of such equipment.
To solve this issue, our yoke frame and bezel were designed based on a high-precision wire winding process and come with the following characteristics;
① They are lightweight, only 1/3 of the existing frames, and smaller.
② The key components of the press are always exposed to compressive stress, so there is no risk of destruction due to the proliferation of crack.
③ The product is stable even under a high amount of load, allowing you to overcome the limits in manufacturing.
Applications
Diffusion Bonding Technology
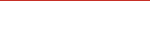
Diffusion bonding is a binding technology that binds solid-state metals or different materials without using any fillers or adhesives.
In this technology, pressure is applied from the two directions (up/down) or from a uniaxial under a high temperature to perform the diffusion bonding or pressurized sintering of the materials.
Energyn has secured the optimal recipes for many materials with many years of process experience and know-how.
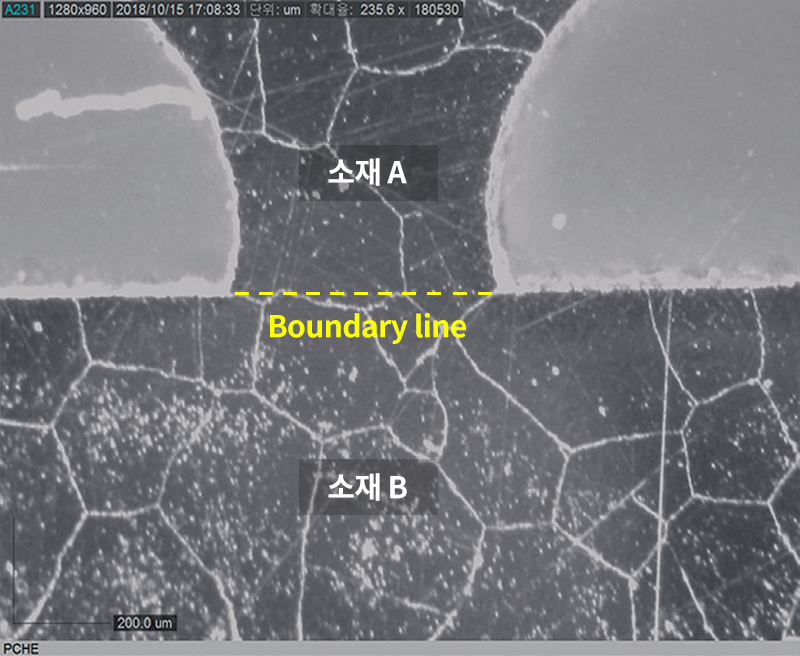
A microscopic glow-up of a diffusion bonding plate
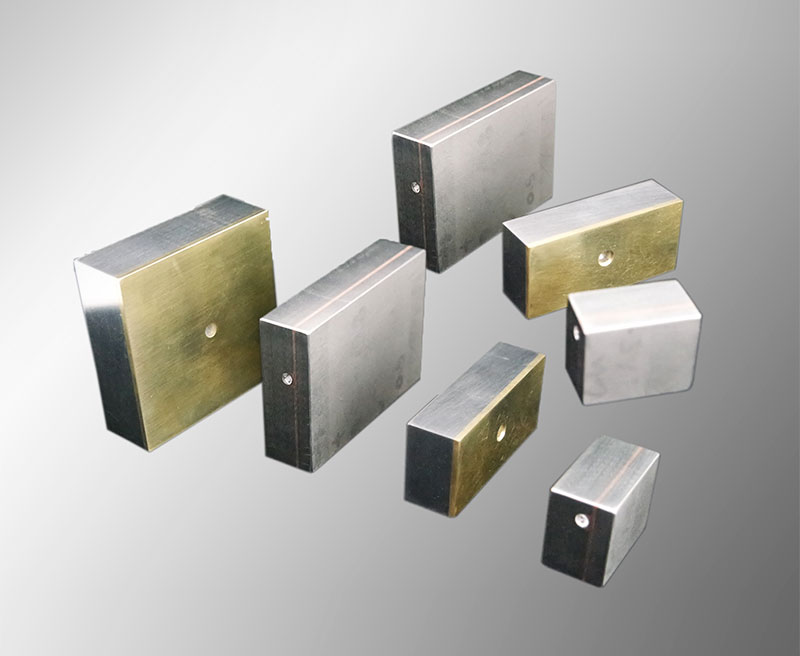
diffusion bonding between different materials
Characteristics
① Can sinter covalent binding Materials which cannot be sintered using normal sintering methods (SiC, Si3N4, B4C, AlN, etc.)
② Can remove pores through the high sintering forth from high pressure.
③ Can completely remove sintering additives or minimize such additives.
④ Powder material is pressure-sintered as hydroxides or carbonates > the ultra-fine particles that are generated as the powder material are disintegrated can be sintered right away.
⑤ Can prevent the disintegration of the sample while sintering.
⑥ Suitable for binding between materials between composite materials that are not optimal for sintering through sintering or expansion.
⑦ The sintered material can have a directional feature depending on the direction of pressurization (uniaxial).
Applications